The Ultimate Guide to Starting Forging: A Detailed Handbook for Emerging Blacksmiths
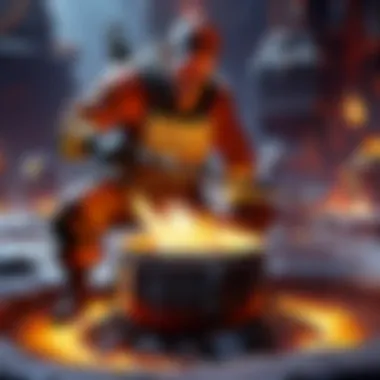

Game Updates and Patch Notes
It is vital to stay updated on the latest developments in the world of blacksmithing. Understanding recent game updates by Blizzard can provide valuable insights into evolving techniques and technologies. By delving into the detailed breakdown of patch notes and changes, aspiring blacksmiths can adapt their forging methods to align with new standards. This analysis goes beyond surface-level observations to explore the impact on gameplay and community feedback, offering a nuanced perspective on the ongoing progression of the craft.
Character Guides and Strategies
In the realm of blacksmithing, mastering specific techniques and approaches is akin to understanding the nuances of individual characters in Blizzard games. Just as gamers seek tips and tricks to enhance their gameplay, aspiring blacksmiths can benefit from in-depth guides that delve into the intricacies of forging. These guides not only cover the fundamental aspects but also provide strategies for honing skills and achieving excellence in the craft. By exploring different playstyles within blacksmithing, individuals can broaden their knowledge and refine their abilities with a strategic mindset.
Community News and Events
The blacksmithing community is a vibrant ecosystem filled with opportunities for growth and collaboration. Similar to community events and tournaments related to Blizzard games, the forging community also organizes gatherings and showcases to celebrate the artistry of metalwork. From highlighting notable achievements to covering fan-made content and creations, there is a sense of camaraderie among blacksmiths akin to the close-knit gaming community. Stay updated on upcoming releases and special events within the blacksmithing sphere to immerse yourself fully in this rich and supportive community.
E-sports and Competitive Scene
While blacksmithing may not have e-sports tournaments like Blizzard games, there is a competitive edge to honing your skills in the craft. By approaching forging with a mindset akin to that of professional gamers, aspiring blacksmiths can elevate their techniques to a competitive standard. Dive into the intricacies of the forging meta, analyze different strategies used by proficient blacksmiths, and draw inspiration from the intensity of competitive gameplay. Just as e-sports enthusiasts dissect matches and player profiles, aspiring blacksmiths can learn from the best and strive for excellence in their craft.
Fan Theories and Lore Discussions
Beyond the physicality of forging lies a realm of storytelling and tradition that mirrors the intricate lore of Blizzard games. Delve into the rich history and mythos surrounding blacksmithing, interpreting its storyline and uncovering hidden secrets within the craft. Engage in discussions that speculate on the evolution of forging techniques and unveil the artistry behind each masterpiece. Just as fan theories add depth to game narratives, exploring the lore of blacksmithing can inspire creativity and innovation, propelling aspiring blacksmiths towards mastery and ingenuity.
Introduction to Forging
Forging is a time-honored craft that holds significant importance in the world of metalworking. Understanding the art of forging is crucial for aspiring blacksmiths, as it lays the foundation for mastering this ancient technique. In this section, we will delve into the history of blacksmithing, the relevance of forging in modern times, and the basic principles that form the core of this craft.
Understanding the Art of Forging
History of blacksmithing
Blacksmithing's history dates back centuries, playing a crucial role in shaping civilizations. The venerable tradition of forging weapons, tools, and decorative items has been a cornerstone of human progress. Exploring the roots of blacksmithing provides insight into the evolution of metalworking techniques and the cultural significance of forged goods. Despite advancements in technology, the art of blacksmithing continues to evoke admiration for its craftsmanship and resilience.
Significance of forging in modern times
In contemporary society, forging retains its relevance by offering unique opportunities for craftsmanship and expression. The authenticity of handcrafted forged items stands out in a mass-produced world, appealing to those who value artisanship and tradition. Modern blacksmiths blend age-old techniques with innovative approaches, creating a fusion of the past and present in their creations. The resurgence of interest in forging reflects a desire for tangible, quality items that tell a story of skill and dedication.
Basic principles of forging
At the core of forging lie essential principles that govern the manipulation of metal through heat and force. Understanding concepts such as heat management, metal deformation, and tool usage form the bedrock of successful forging endeavors. Mastery of these fundamental principles equips blacksmiths with the knowledge to transform raw materials into functional and decorative pieces. While basic in theory, the principles of forging require precision and practice to execute effectively, setting the standard for craftsmanship in the forge.
Essential Tools and Equipment
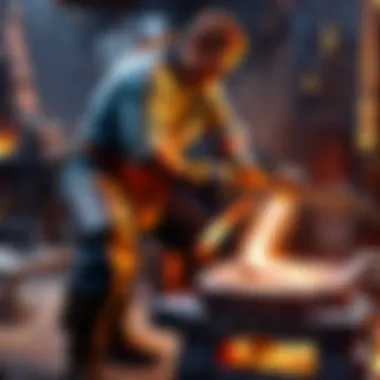

Transitioning from theory to practice necessitates a comprehensive understanding of the tools and equipment essential for forging. The anvil and hammer, tongs and vice, as well as the forge and fuel play integral roles in the blacksmith's workshop. Each tool serves a specific purpose, contributing to the success and efficiency of the forging process.
Anvil and hammer
Among the most recognizable symbols of blacksmithing, the anvil and hammer form the cornerstone of the forge. The anvil provides a sturdy surface for shaping metals, while the hammer delivers controlled strikes to manipulate the material. The collaboration between anvil and hammer exemplifies the synergy between precision and force, essential for forging intricate and durable pieces. Despite their simplicity, the anvil and hammer represent centuries of refining design and function in the blacksmithing trade.
Tongs and vice
Tongs and vice offer the blacksmith a firm grip on the hot metal, ensuring precise handling during forging operations. The versatile nature of tongs allows for the manipulation of various shapes and sizes of metal pieces, enhancing the smith's flexibility in creating diverse objects. Similarly, the vice provides stability and support when working on intricate details or when applying significant force to the metal. Together, tongs and vice form indispensable components of the blacksmith's tool arsenal, enabling safe and efficient forging practices.
Forge and fuel
Central to any forge operation, the forge and fuel source determine the heat output and atmosphere required for successful forging. Whether utilizing a traditional coal forge or a modern gas forge, the choice of forge impacts the forging process's speed and efficiency. Equally important is the selection of fuel, with coal, propane, and natural gas offering varying heat intensities and burning characteristics. The forge and fuel combination represents the heart of the forge, providing the necessary heat to transform raw metal into functional works of art.
Materials Used in Forging
The selection of materials in forging significantly influences the outcome of the smith's work, determining properties such as strength, durability, and aesthetic appeal. From mild steel to high-carbon steel, as well as alloys and specialty metals, the options for blacksmiths are diverse and impactful.
Mild steel
Mild steel, known for its malleability and ease of manipulation, serves as a popular choice for novice and experienced blacksmiths alike. Its affordability and versatility make it ideal for practicing fundamental forging techniques and experimenting with different designs. While lacking the hardness of high-carbon steel, mild steel accommodates a wide range of projects, from decorative pieces to functional tools, making it a staple in the blacksmith's repertoire.
High-carbon steel
Renowned for its strength and durability, high-carbon steel stands as a preferred option for creating tools and blades requiring superior hardness and edge retention. The high carbon content in this steel variant offers increased wear resistance and sharpness, ideal for producing cutting implements and precision instruments. With proper heat treatment and forging techniques, high-carbon steel yields exceptional results, perfect for demanding applications in various industries.
Alloys and specialty metals
For intricate and specialized forging projects, alloys and specialty metals provide unique properties and characteristics that cater to specific requirements. Alloys like stainless steel and brass offer corrosion resistance and aesthetic appeal, making them popular choices for decorative and functional pieces. Specialty metals such as titanium and tantalum introduce exceptional strength-to-weight ratios and exotic appearances, expanding the creative possibilities for skilled blacksmiths seeking to push the boundaries of traditional forging practices. Incorporating alloys and specialty metals into forging projects elevates the craftsmanship and allure of the final creations.
Setting Up Your Forge
Setting up your forge is a crucial aspect when embarking on the journey of blacksmithing. The forge serves as the heart of any blacksmith's workspace, where metal is heated to its malleable state for shaping and crafting. It is imperative to consider several specific elements and benefits when setting up your forge, ensuring an efficient and safe working environment for your forging endeavors.
Choosing the Right Location
In the process of setting up your forge, selecting the right location plays a pivotal role in the overall success of your blacksmithing operations. Ventilation and safety considerations are paramount factors to contemplate. Adequate ventilation is essential to dissipate fumes and maintain a healthy respiratory environment within the workspace. Integrating proper safety measures reduces the risk of accidents and ensures a secure forging space.
Space requirements also demand attention when establishing your forge. Sufficient space allows for comfortable movement around the forge and accomodates the positioning of essential equipment without restrictions. A well-organized workspace enhances productivity and fosters a conducive environment for creativity and precision in forging activities.
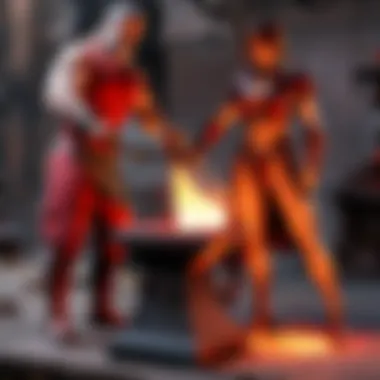

Heat management is a key consideration to optimize your forging experience. Efficient heat distribution within the forge is critical for achieving desired metalworking temperatures. By implementing effective heat management strategies, you can regulate the temperature necessary for various forging techniques, guaranteeing consistent results in your metalwork.
Building or Buying a Forge
When deciding on whether to build or purchase a forge, understanding the types of forges available is essential. Different forges cater to varying needs and preferences, such as gas forges, coal forges, or electric forges. Each type possesses unique characteristics that impact their performance and suitability for specific forging tasks.
For individuals inclined towards a hands-on approach, DIY forge construction tips offer valuable insights into creating a custom forge. Tailoring the forge to meet your requirements enables a personalized blacksmithing experience and fosters a deeper connection with your tools and workspace. Alternatively, purchasing commercial forges provides convenience and expediency, offering pre-made solutions that align with established industry standards.
Organizing Your Workspace
Organizing your workspace plays a significant role in optimizing efficiency and functionality within your forge. Proper tool storage and accessibility are imperative for streamlining workflow and maintaining a clutter-free environment. Accessible tools enhance the efficiency of forging processes and reduce downtime associated with tool retrieval.
Careful consideration of workspace layout contributes to the overall ergonomics and flow of forging activities. An optimal layout ensures that workstations and equipment are strategically positioned to facilitate smooth transitions between tasks. A well-thought-out workspace layout enhances productivity and minimizes unnecessary movements, promoting a seamless forging experience.
Adequate lighting is a critical component of a well-equipped forge. Proper lighting not only enhances visibility for intricate forging tasks but also creates a safe working environment by minimizing potential hazards. Adequate lighting sources positioned strategically within the workspace prevent eye strain and promote precision in metalworking tasks.
Basic Forging Techniques
In the realm of blacksmithing, mastering basic forging techniques is paramount to sculpt raw metal into intricate works of art. Understanding the nuances of drawing out, bending, twisting, and joining metals elevates the craft to a realm of precision and creativity. Basic forging techniques form the backbone of every blacksmith's skill set, serving as the foundation upon which complex creations are built.
Drawing Out and Upsetting
Drawing out metal involves elongating a piece, making it thinner and longer. It is a fundamental technique that allows blacksmiths to manipulate the shape and size of the metal. By carefully heating metal at selective points, drawing out enables craftsmen to create tapered ends or elongated sections for various applications. This technique's versatility lies in its capacity to transform solid pieces of metal into intricate forms, essential for crafting tools, weapons, and decorative elements.
Bending and Twisting Metal
Bending metal accurately requires a keen understanding of heat manipulation and pressure application. The proper bending procedure ensures that metal curves smoothly without deformities or cracks. Conversely, twisting metal involves rotating it along its axis to create spiral or helical shapes. These techniques add an artistic dimension to metalwork, allowing artisans to infuse fluidity and movement into their creations. Whether shaping handles, decorative elements, or structural components, mastering bending and twisting techniques expands a blacksmith's design repertoire.
Joining Metal Pieces
When it comes to joining metal pieces, blacksmiths must choose between welding and brazing. While welding involves creating a permanent bond between metals by melting their surfaces, brazing uses a lower melting point material as a filler to join components. Forge welding, a specialized form of welding conducted at high temperatures in a forge, produces strong and durable joints. Learning the nuances of each method equips blacksmiths with the expertise to create robust connections in their metalwork. Tips for ensuring strong joints include proper surface preparation, suitable filler material selection, and precise heat control to achieve metallurgical cohesion.
Advanced Forging Skills
When delving into the realm of blacksmithing, mastering advanced forging skills becomes paramount for aspiring blacksmiths seeking to elevate their craft. The essence of advanced forging skills lies in the intricate techniques and nuanced processes that allow blacksmiths to create intricate and durable metalwork. From pattern welding to forge welding, these skills enable artisans to manipulate metal with precision and artistry, paving the way for unique and stunning creations. Understanding the complexities of advanced forging skills empowers blacksmiths to push their creative boundaries and craft exceptional pieces that showcase their expertise and dedication to the age-old craft.
Pattern Welding and Forge Welding
Creating patterned metal
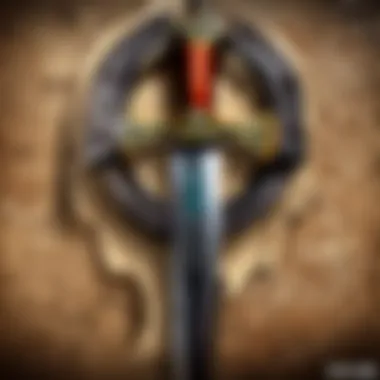

Pattern welding, a captivating technique that involves forging layers of different metals to create mesmerizing patterns, holds a special place in the world of blacksmithing. This method not only enhances the visual appeal of the final piece but also improves its strength and durability. By skillfully combining various metals and manipulating them through heat and hammer, blacksmiths can produce distinct patterns that add a unique aesthetic dimension to their work. The versatility and strength of patterned metal make it a popular choice among blacksmiths aiming to create exceptional pieces that stand out in the forging community.
Step-by-step guide to forge welding
Forge welding, a fundamental aspect of blacksmithing, plays a crucial role in joining metal pieces seamlessly and securely. This detailed process involves heating the metal to a high temperature until it reaches a malleable state, enabling blacksmiths to hammer and shape it effectively. By following a systematic sequence of heating, joining, and hammering, artisans can achieve strong and durable welds that withstand the test of time. The step-by-step nature of forge welding ensures precision and efficiency, allowing blacksmiths to create intricate and reliable structures that form the foundation of their metalwork.
Pattern welding techniques
Exploring various pattern welding techniques opens up a world of creative possibilities for blacksmiths passionate about pushing the boundaries of their craft. From twist patterns to mosaics, each technique offers a unique way to infuse personality and character into metalwork. By understanding the intricate process of pattern welding and experimenting with different methods, blacksmiths can develop a signature style that sets their creations apart. The fusion of tradition and innovation in pattern welding techniques allows artisans to craft pieces that resonate with both heritage and contemporary aesthetics, making each creation a masterpiece of skill and artistry.
Tool and Blade Making
Efficient tool and blade making techniques are essential for blacksmiths aiming to create functional and reliable implements that serve various purposes. From heat treating tools and blades to considering design aspects and adding finishing touches, every step in the making process contributes to the quality and longevity of the final product. By mastering these essential skills, blacksmiths can produce tools and blades that not only perform exceptionally but also showcase their dedication to craftsmanship and precision.
Heat treating tools and blades
Heat treating stands as a critical stage in the tool and blade making process, where the metal undergoes controlled heating and cooling to enhance its hardness and durability. By subjecting the metal to specific temperatures and quenching it in various mediums, blacksmiths can manipulate its molecular structure, ensuring optimal performance. The meticulous nature of heat treating demands precision and expertise, as even slight deviations can impact the quality and functionality of the final tool or blade. By mastering the art of heat treating, blacksmiths can create implements that excel in strength, sharpness, and resilience.
Design considerations
Design considerations play a pivotal role in determining the functionality, aesthetics, and ergonomics of tools and blades. From selecting appropriate materials to optimizing shapes and sizes, every design decision influences the overall performance of the final product. By paying attention to details such as handle ergonomics, weight distribution, and cutting edge geometry, blacksmiths can tailor their creations to meet specific needs and preferences. Embracing thoughtful design elements not only enhances the performance of tools and blades but also elevates the artistic value of the finished piece, making it a harmonious blend of form and function.
Finishing touches
Adding finishing touches to tools and blades not only imparts a polished look but also ensures durability and corrosion resistance. From polishing surfaces to applying protective coatings, the final steps in the making process contribute to the overall quality and aesthetics of the tool or blade. By meticulously refining edges, engraving decorative motifs, and buffing surfaces to a lustrous sheen, blacksmiths can elevate their creations from functional tools to works of art. The importance of finishing touches lies in the attention to detail and craftsmanship they exemplify, showcasing the blacksmith's dedication to excellence and passion for their craft.
Artistic Forging and Sculpting
Artistic forging and sculpting open a realm of creativity and expression for blacksmiths eager to explore the aesthetic potential of metalwork. By venturing into creative forging techniques, honing sculpting skills, and incorporating artistic elements into their creations, artisans can breathe life and personality into their metal pieces, transforming raw materials into captivating works of art.
Exploring creative forging techniques
Creative forging techniques foster innovation and experimentation, encouraging blacksmiths to break free from traditional constraints and explore new possibilities. By manipulating metal through unconventional methods, such as texturing, folding, or asymmetrical shaping, artisans can infuse their creations with a sense of depth and character. The exploration of creative forging techniques not only expands the artistic horizons of blacksmiths but also challenges them to push the boundaries of traditional craftsmanship, resulting in unique and compelling works that resonate with viewers.
Tips for sculpting metal
Sculpting metal requires a delicate balance of skill, vision, and patience, as artisans shape raw materials into intricate forms and structures. By employing precise hammer blows, controlled heat applications, and keen observational skills, blacksmiths can breathe life into metal, transforming it into fluid shapes and expressive compositions. The art of metal sculpting lies in the sculptor's ability to capture movement, emotion, and detail in solid form, creating pieces that captivate and inspire audiences with their elegance and artistry.
Incorporating artistic elements
Weaving artistic elements into metalwork elevates pieces from mere objects to storytelling artifacts that communicate meaning and emotion. Whether through symbolic motifs, intricate embellishments, or thematic narratives, artistic elements add layers of depth and significance to metal creations. By infusing personal style, cultural influences, or historical references into their work, blacksmiths can create pieces that resonate on both aesthetic and intellectual levels, inviting viewers to engage with the work on multiple dimensions. The integration of artistic elements not only showcases the blacksmith's creative vision and technical skill but also transforms metalwork into a medium for profound expression and dialogue.
Emergency response procedures outline the steps to take in the event of unforeseen incidents, empowering blacksmiths to react swiftly and decisively in emergencies. By establishing clear protocols and regularly practicing emergency responses, blacksmiths can mitigate the impact of accidents and prioritize the safety of all individuals in the workspace.
Precautions for handling hot metal emphasize the importance of cautious and deliberate actions when working with heated materials. From using specialized tools for handling hot metal to employing proper gripping techniques, these precautions not only safeguard against injuries but also optimize the forging process, allowing for precise and controlled metal manipulation. By adhering to safety measures and maintenance protocols, aspiring blacksmiths can cultivate a secure and sustainable forging practice, laying the foundation for a successful journey in the craft of blacksmithing.