Essential Tools and Skills for Blacksmithing
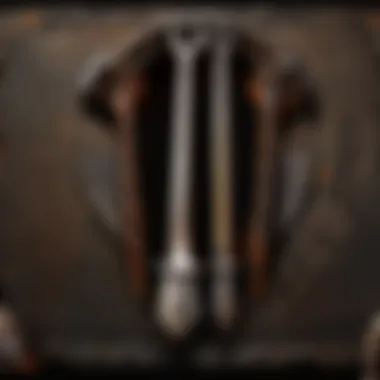

Intro
Blacksmithing has long captivated those with a penchant for craftsmanship. This age-old trade requires a unique blend of tools, materials, and techniques. At its core, blacksmithing is about shaping metal through heat and hammering, an art that combines technical skill with creativity. Whether you are a beginner eager to forge your first tool or an experienced smith looking to refine your craft, understanding the essentials is crucial.
Mastering blacksmithing involves more than just swinging a hammer. It’s about creating a dedicated space, knowing your tools, using quality materials, and implementing safety practices. This article aims to demystify the blacksmithing process, offering insights into setting up a workshop and honing your skills.
The significance of blacksmithing in history cannot be overstated. From crafting weapons in ancient times to producing modern decorative art, the role of the blacksmith remains vital. As we navigate through this guide, we’ll explore everything you need to know to start your journey into this fascinating world of metalworking. Armed with the right knowledge, anyone can delve into blacksmithing with confidence and skill.
Game Updates and Patch Notes
In the realm of blacksmithing, there aren’t frequent updates like one might find in an online game. However, trends and techniques ebb and flow over time, influenced by both technological advancement and community insight.
Overview of Recent Methods
Around the blacksmithing community, one can observe a great transformation in methods, tools, and materials which get introduced or refined. New forms of forges, like the propane-powered forges, are gaining popularity for their efficiency, pushing the traditional coal-burning forges into the background, but not entirely disappearing. Many purists still prefer that smoky ambiance for the authenticity it brings.
Detailed Breakdown of Tools
- Anvil: The heart of any blacksmith’s workshop. Recent innovations have produced various types of anvils which suit specific forging needs.
- Hammer: A blacksmith's best friend. The choice of hammer can significantly affect the final product's quality, with various weights and shapes tailored for different tasks.
- Tongs: Essential for holding hot metal, tongs come in various designs to suit different shapes and sizes.
- Forge: The heating source for metalwork. Gas or electric forges have been a trend, providing more precise control over temperatures.
Analysis of Impact on Craftsmanship
The introduction of these modern tools has shifted how blacksmiths approach their work. While traditional methods and tools will always hold value, the efficiencies gained with new technology have allowed smiths to focus more on creativity and less on labor-intensive processes. Balancing tradition with innovation seems to be the prevailing theme within the community.
Setting Up Your Workshop
When diving into blacksmithing, the workshop setup is paramount. Safety should be your first priority, followed closely by organization and accessibility of tools.
- Space: A well-ventilated area is essential. Keep flammable materials at a safe distance.
- Tool Organization: Having a system for tools keeps everything at hand. Consider pegboards or tool chests.
- Safety Equipment: Equip your workshop with gloves, goggles, and a fire extinguisher.
In summary, establishing a blacksmithing workshop is like laying a solid foundation for a house—it pays off in both comfort and efficiency. Keeping everything organized lets you focus on your creations without the hassle of searching for that misplaced hammer.
Blacksmithing is not just about forging metal; it’s about forging one’s skills and creativity.
End
Blacksmithing is a craft that melds tradition with personal expression. By understanding the essentials—from tools to techniques—anyone can begin their journey into this ancient art. Armed with knowledge and a dedicated workspace, the possibilities are endless. Whether crafting tools, art, or heirlooms, the satisfaction derived from the fruits of labor will keep the fire burning bright, compelling you to continually refine your skills.
Prolusion to Blacksmithing
Blacksmithing is an ancient craft that intertwines art with utility. For many, it’s not just about shaping metal; it’s about connecting with a tradition that stretches back thousands of years. In this article, we will peel back the layers of this enthralling trade, exploring the historical developments, the tools that have evolved over time, and the still-thriving practices that define blacksmithing today. Understanding the intricacies of blacksmithing can illuminate one's appreciation for metalwork, whether one wishes to partake in it as a hobby or as a professional pursuit.
Historical Context of Blacksmithing
From the dawn of civilization, blacksmithing has played a pivotal role in societal advancement. In ancient times, blacksmiths were revered figures, essential in crafting tools, weapons, and various implements crucial for survival. Skills passed from father to son, hidden in workshops that exuded the heat of the forge and the smells of metalworking. A famous historical figure, John F. Kennedy once reflected on the intimate bond shared between a blacksmith and his craft: "The future is not a gift; it is an achievement." This rings truer than ever; blacksmithing is not merely about physical shaping but is a heritage in its own right.
Historically, the transition to iron and eventually steel transformed blacksmithing profoundly. Ancient civilizations from the Egyptians to the Romans utilized iron for improved agricultural tools. The Middle Ages further saw the emergence of specialized blacksmiths who would create ornate pieces alongside practical items. Iron became the backbone of everyday lives, leading to architectural marvels and advancements in warfare.
Modern Blacksmithing Practices
Fast forward to today, and blacksmithing has undergone a renaissance. Modern smiths blend traditional techniques with contemporary design, allowing for an explosion of creativity. The craft has adapted, welcoming innovations that enhance productivity and safety. With the rise of the internet, there’s been a notable shift; workshops are no longer confined to lonely regions. Today’s blacksmiths often connect through forums like reddit.com, exchanging knowledge and showcasing innovative works.
In modern practices, you’ll find blacksmithing utilized in art as much as in utility. Artists like Robert G. Pritchard shape metal into intricate sculptures, using techniques layered with generations of wisdom. Additionally, the sustainability movement has gained traction in blacksmithing, with many smiths advocating for the use of recycled metals, embodying a philosophy of minimizing waste.
Thus, the landscape of blacksmithing encompasses more than just iron and fire; it embodies the continuity of craft, communal learning, and an ever-evolving art form. Understanding this modern context lays a solid foundation for any aspiring smith, allowing them to step into a workshop that feels both ingeniously innovative and steeped in history.
Essential Tools for Blacksmithing
Blacksmithing, with its roots deep in history, thrives on a foundation built upon essential tools. Understanding these tools is crucial for anyone venturing into the craft, from those just getting their feet wet to seasoned artisans looking to refine their method. Each tool plays a vital role not just in the creation of metal works but also in your safety and efficiency while working.
Forge: The Heart of Blacksmithing
At the heart of every blacksmith's operation is the forge. This is where the magic happens. A forge's primary purpose is to heat metal until it’s malleable, allowing the smith to shape it with the tools at hand. The type of forge can vary widely; some smiths prefer coal for its intense heat, while others veer toward propane for convenience and cleaner operation.
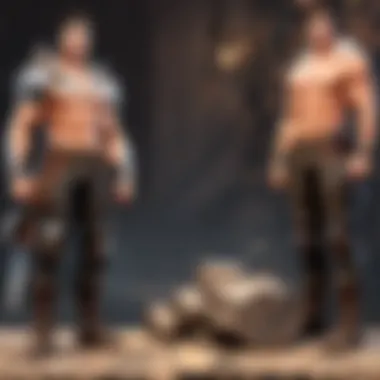

Ultimately, the choice will depend on your specific needs, projects, and accessibility to materials. A durable forge ensures better heat retention and efficiency.
"In blacksmithing, a quality forge isn't just a tool; it's an artist's canvas that brings metal to life."
Anvil: A Crucial Component
Following closely is the anvil—often regarded as one of the most recognizable symbols of blacksmithing. This sturdy fixture serves as the work surface where the heated metal is shaped and hammered into its desired form. An important consideration in selecting an anvil is the weight. A heavier anvil can absorb hammer blows better, resulting in cleaner work and less vibration.
The material matters too. Traditional anvils are made of steel, providing durability and strength necessary for handling extensive metalworking tasks. Each time you strike the anvil, you're not only forming the metal but creating objects that may last generations, bridging the gap between the past and present.
Hammers: Varieties and Their Uses
When it comes to hammers, the choices are plentiful, and each type has its significant advantages. A blacksmith may use a variety of hammers in their work, including:
- Ball Peen Hammer: Great for rounding edges or driving tools.
- Claw Hammer: Best for general-purpose, especially helpful in coarse tasks.
- Cross-Peen Hammer: Excellent for drawing out metal and working on thin sections.
Each hammer, with its unique design, enables different techniques. A slight change in the hammer's shape can lead to significant differences in the outcome.
Tongs: Types and Techniques
Tongs are the hands of the blacksmith without a doubt. Given the intense heat that metal reaches, tongs keep fingers safe while maneuvering workpieces. There are specialized tongs for different shapes and sizes of metal. Understanding the types of tongs is critical;
- Flat Tongs: Ideal for gripping flat stock.
- Round Tongs: Perfect for pipes and round bar stock.
- V-Bit Tongs: Facilitates working with irregular shapes.
Learning how to use tongs effectively is as vital as mastering the hammer. It takes practice and know-how to ensure you’re not just gripping but controlling the metal with precision.
Quenching and Tempering Tools
Finally, there is the aspect of quenching and tempering, which can make or break your final product. Quenching is the process of rapidly cooling heated metal, typically in water or oil, which hardens the material. The effectiveness of this process depends on having proper tools on hand, such as:
- Quench Tanks: Containers specifically designed for quick cooling.
- Thermometers: For precise temperature control to ensure consistency.
- Protective Equipment: To safeguard against splashes and hot metal.
Once quenched, tempering—a reheating process—allows you to reduce brittleness in the hardened metal, making your tools and creations more durable for everyday use. Knowing how and when to apply these processes requires practice and an understanding of the materials you’re working with.
In summary, the essential tools of blacksmithing, from the forge and anvil to the various hammers and tongs, play a crucial role in shaping metal. Each tool is intertwined with the others, forming a cohesive unit that transforms raw metal into functional or aesthetic masterpieces.
Materials Needed for Blacksmithing
When it comes to blacksmithing, the materials you choose are just as essential as the tools and techniques you employ. Without the right materials, even the most skilled blacksmiths can find themselves at a loss, struggling to create quality work. This section dives into the different types of metals, the role of alloys, and the fuels necessary for successful forging.
Different Types of Metals
Understanding the properties of various metals can make or break the final piece. Steel, for instance, is the king of blacksmithing. It’s versatile, strong, and can be combined with other elements to bring out a variety of characteristics – depending on what you need. Below are some common metals you will encounter:
- Mild Steel: Known for its ease of use and ductility, mild steel is a favorite for beginners. It can be shaped easily and is often used for functional items and artistic statements alike.
- Tool Steel: This is harder than regular steel and designed for manufacturing tools. Brands like O1 and A2 are what you’d want for made-to-last pieces. Requires good knowledge for proper usage.
- Stainless Steel: Even though it’s trickier to work with, its corrosion resistance makes it ideal for items exposed to moisture, like kitchen tools.
- Aluminum: Lightweight and resistant to rust, aluminum is often used for decorative elements. Just know it requires different methods compared to steel.
Each metal has its nuances, so it’s essential to pick wisely based on your project.
Alloys: When and Why
Alloys are quite the interesting subject in blacksmithing. They're created by combining two or more metals to enhance their properties. Here’s why alloys matter:
- Stronger and Tougher: Mixtures like steel, which includes iron and carbon, can provide a unique balance between flexibility and durability.
- Special Characteristics: Some alloys have specific uses which make them apt for certain products. For instance, bronze—an alloy of copper and tin—is known for its resistance to corrosion. This versatility can be unparalleled in artistic pieces or historical reproductions.
- Cost Efficiency: Sometimes, using a cheaper base metal and mixing it with a small amount of a premium metal can yield satisfactory results without breaking the bank.
Choosing the right alloy for a project often depends on multiple factors, such as the environment the final piece will endure or the specific qualities needed in its form.
Fuels for Forging
The fuel you use in your forge can dictate the heat level and consistency of your work. Here are the predominant types of fuel used:
- Charcoal: Preferred by many traditional blacksmiths, charcoal creates a clean burn and reaches high temperatures. It’s also easier on the environment compared to fossil fuels.
- Coal: Bituminous coal is another classic choice. It burns hotter than charcoal but requires more management to maintain optimal conditions.
- Propane: Increasingly popular among modern smiths, propane delivers a clean and consistent heat. It’s user-friendly, particularly for those starting out.
- Wood: A traditional choice for beginners; it requires skill to manage temperatures effectively.
Each of these fuels has its advantages and considerations, so it’s crucial to find one that aligns with your needs and matches your workflow.
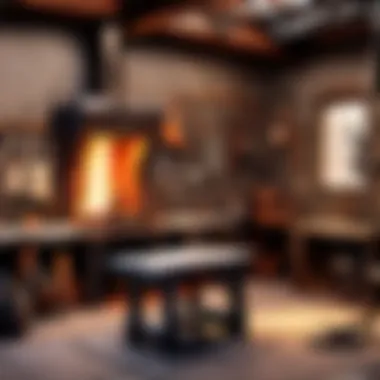

"In blacksmithing, the right materials set the foundation for artistry and functionality, guiding you to create not just objects but pieces of soul."
Setting Up a Blacksmithing Workspace
Setting up a blacksmithing workspace is not just about having the tools and space; it's about creating an environment where creativity meets safety. A well-planned workspace can make a world of difference in the way you approach your projects. The importance of choosing the right location, enforcing safety measures, and keeping your tools organized is paramount. Each aspect plays a unique role in ensuring efficient workflow and cultivating your skills as a blacksmith.
Selecting an Appropriate Location
The first step in creating a workspace involves finding a suitable location. Ideally, this should be a place where noise and heavy work don't disturb others. An outdoor setup can be ideal, especially for those who work with charcoal or forge. However, don’t overlook the importance of shelter. A solid roof means you won’t be halted by a rainstorm.
Consider also the proximity to electrical outlets if you’re using power tools. Ventilation is key—without good airflow, you'll quickly find that smoke and fumes can cloud your creativity and even become a health hazard. Proper drainage can also prove beneficial, especially when mixing materials or cleaning up after a busy session. Remember, you want a space that invites ideas and encourages the physical creation of those ideas.
Safety Measures in the Workshop
Safety should be at the forefront of any blacksmithing endeavor. The heat from the forge can turn a casual setting into a perilous zone in an instant. Wearing safety gear such as gloves, goggles, and aprons is non-negotiable—this is your first line of defense against sparks and hot materials.
Some key safety measures include:
- Installing fire extinguishers in visible locations.
- Ensuring first aid kits are stocked and accessible.
- Keeping a safe distance between tools and flammable materials.
- Using a flame-retardant mat around work areas to contain stray sparks.
"An ounce of prevention is worth a pound of cure. In blacksmithing, it could save your workshop—and perhaps your health."
Adopting this safety mindset helps create a work environment where you can focus on the craft, rather than constantly worrying about the potential setbacks.
Organizing Tools and Materials
Once you've nailed down the location and ensured safety, organizing your tools and materials can do wonders for productivity. A cluttered space can lead to confusion and even accidents, whereas a well-organized workshop allows you to find what you need when you need it.
Start with a solid layout. Tools should be easily accessible but stored thoughtfully. For instance:
- Group similar tools together. Keep hammers, chisels, and other hand tools within arm's reach.
- Label drawers or sections. This will save you time sifting through everything.
- Use storage solutions. Hook racks for tongs, magnetic strips for smaller metal pieces, and dedicated bins for different metal types are practical options.
Additionally, consider a maintenance routine. Regularly cleaning tools and checking for wear can extend their lifespan and keep your workspace productive. An organized space fosters creativity and efficiency, allowing you to concentrate fully on the art of blacksmithing.
Basic Techniques in Blacksmithing
In the world of blacksmithing, mastering basic techniques is vital for forging a strong foundation in metalworking. These skills not only enable a smith to manipulate metal effectively but also to create artistry in their craft. The significance of these fundamental techniques cannot be undersold, as they determine the quality and consistency of the final products.
Forging: Techniques and Processes
Forging is central to blacksmithing and involves the heating of metal to a malleable state and then shaping it using force. This can be accomplished through various methods:
- Hammering: The essence of forging often lies in hammering. A smith will deliver precise blows to shape the metal as needed. The blow's intensity and angle can change the outcome drastically.
- Drawing Out: This technique essentially elongates the metal. A smith applies force to the bill of the metal, reducing its thickness and increasing its length. This process is crucial for making tool blades or elongating components.
- Upsetting: This involves shortening a piece of metal by increasing its diameter. Smiths typically use this when they need to create end points or thicker sections on rods.
The sound of metal striking metal creates a rhythm that bears witness to skill and experience. Getting the right temperature is also vital. Overheating can degrade the metal’s integrity, while underheating makes it tough to shape. A careful balance is essential.
Welding in Blacksmithing
Welding is a technique that joins two or more pieces of metal together, and it can be achieved through heat and pressure. Here are some key approaches:
- Forge Welding: This ancient technique involves heating the metals to a high temperature and then hammering them together. It requires precision and timing. The art lies in getting the correct temperature before the hammer meets the metal, leading to a solid bond.
- TIG and MIG Welding: Though more modern, these methods showcase how welding has evolved. While TIG offers fine control, MIG is known for speed and adaptability. Understanding both helps a blacksmith expand their repertoire and tackle more complex projects.
Welding isn’t just about joining equipment; it’s a way to create beautiful art pieces or practical tools that might be otherwise impossible to make. Knowing when to weld can be the difference between a good piece and a great one.
Finishing Techniques: Creating a Smooth Surface
Finishing techniques are where the smith’s vision really comes to life. Achieving a smooth surface isn't merely a cosmetic choice but also enhances durability. Here are some common methods:
- Grinding: This method uses an abrasive wheel to smooth out jagged edges. It’s beneficial for creating precise and clean finishes. The key is to maintain an angle that doesn’t cause overheating.
- Polishing: A higher level of finishing that often involves buffing your work with softer materials. It not only brings out the visual appeal but also can help protect the finish against rust.
- Texturing: Sometimes, a rough finish can add character. Techniques like sandblasting can introduce unique textures that make each piece distinctive and personal.
"The journey in blacksmithing teaches patience and precision, fundamental qualities for mastering your craft."
The importance of basic techniques in blacksmithing cannot be overstated. They are an artisan’s toolkit that will pave the way for creativity and proficiency. Mastery of these basic techniques will enhance not only the quality of work but will also elevate the blacksmithing experience as a whole.
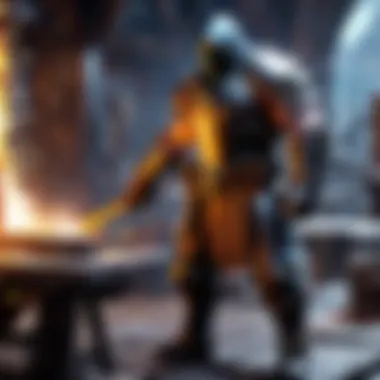

Developing Skills as a Blacksmith
Mastering the art of blacksmithing goes beyond just knowing how to swing a hammer. It involves a series of skills that culminate in the ability to transform metal into useful and aesthetic items. Developing these skills is essential for anyone serious about blacksmithing, whether you're a complete novice or someone with a bit of experience. It's a process that brings not just technical proficiency but also a deeper appreciation for the materials and practices involved.
Resources for Learning Blacksmithing
For those eager to hone their craft, a plethora of resources is available that cater to varying skill levels. Books remain a reliable choice. "The Complete Modern Blacksmith" by Alexander G. Weygers is a classic for anyone wanting foundational knowledge. More contemporary guides like "Blacksmithing Basics for Beginners" by Lorelei Sims offer step-by-step projects that are easy to follow.
Online platforms have also exploded in recent years. Websites like reddit.com provide forums where both amateurs and veterans share advice. Additionally, free video tutorials on platforms like YouTube can help illustrate techniques. For instance, channels such as Black Beard Projects showcase everything from forge setup to intricate finishing techniques.
Workshops and blacksmithing schools also present excellent opportunities for hands-on learning. Places like the John C. Campbell Folk School offer courses, making the experience interactive and practical. Local groups often have workshops, so it’s wise to keep an ear to the ground.
Practice Projects for Beginners
When starting out in blacksmithing, it's crucial to have projects that build confidence while enhancing skills. Here are a few projects beginners might want to consider:
- Hooks: Simple and practical, making hooks can help you grasp basic hammering techniques and the properties of the metal.
- Nails: Crafting nails requires precision—an important skill that lends itself well to more complex projects down the line.
- S-hooks: This project allows you to practice bending and shaping, useful skills that are the backbone of many blacksmithing tasks.
- Simple Knife: Once comfortable, creating a basic knife can infuse a sense of accomplishment and show tangible results of your efforts.
"Start small, aim big. Each project is a stepping stone to mastering the art of blacksmithing."
It's commendable to approach each endeavor with patience. It's through repeated practice that muscle memory develops, and skills begin to stick.
Advanced Techniques and Styles
As you gain confidence in your abilities, you may wish to dive into advanced techniques which can vary significantly depending on your interest—be it artistic blacksmithing, sword making, or tool creation. Some advanced techniques to consider:
- Damascus Steel Making: This traditional method of forging combines different metals to create a unique pattern and can yield high-quality blades.
- Rivet Forging: Understanding how to create and shape rivets expands your assembly skills and is often used in larger projects like gates or frames.
- Mokume Gane: Originating from Japan, this involves layering different metals to create beautiful patterns, often used in jewelry making.
Employing these techniques requires a solid grasp of the fundamentals. It’s important to attend specialized classes or workshops focusing on these skills. Many blacksmiths have favorite styles that reflect personal taste or historical influences, which can further deepen your journey into the craft.
In summary, developing skills in blacksmithing is a continual journey that thrives on practice, knowledge, and exploration. Taking advantage of available resources, engaging in practical projects, and experimenting with advanced techniques will not just improve your skills; it will also enrich your understanding of metalworking as an art form.
Common Challenges in Blacksmithing
Blacksmithing, while a rewarding and artistic craft, is not without its share of challenges. For both newcomers and seasoned artisans alike, understanding these hurdles is vital for not just mastering the craft, but also enjoying the process. This section explores the common challenges in blacksmithing, emphasizing mistakes to avoid and common failures that can stymie progress.
Mistakes to Avoid
Mistakes in blacksmithing can lead to wasted materials, time, and sometimes even frustration. Here are some pitfalls to keep in mind:
- Ignoring Material Properties: Each type of metal behaves differently under heat and pressure. Not understanding these nuances can result in inappropriate tool selection or ineffective techniques. For example, trying to forge stainless steel with a technique suited for wrought iron might end in disaster.
- Inadequate Tool Maintenance: Failing to care for your tools can diminish their effectiveness. Regularly check and maintain your anvil and hammers to ensure they are in prime condition. A chipped hammer face or a rusty anvil can lead to sloppy work and may ultimately ruin a project.
- Poor Heat Management: This is one of the most critical aspects of blacksmithing. Heating metal correctly is an art in itself. Too hot and you risk burning through the material; too cool and it won’t shape properly. Finding that sweet spot requires keen observation and practice.
- Neglecting Safety Practices: Safety must never take a backseat in the shop. Dismissing the importance of proper gear, such as goggles and gloves, not only puts oneself at risk but also sets a bad habit that could affect others.
Remember, each mistake is a stepping stone. Approach them with curiosity, not defeat.
Understanding Common Failures
Failure is part of the journey in blacksmithing. Here are some typical failures one might encounter:
- Cracks in Metal: This often occurs when the metal is not heated evenly or when it is forged too quickly. Learning to recognize the signs of overheating or temperature gradients is crucial for avoiding cracks.
- Inaccurate Shapes: If a smith rushes the forging process or fails to properly support the metal, they might end up with pieces that are warped or not to specification. Take the time to check dimensions and shapes throughout the process.
- Bad Welds: A proper weld is strong and stable. If it fails, it usually comes down to improper temperature or cleanliness of the metals being joined. Always make sure surfaces are clean and you maintain the right heat during welding.
- Warping During Quenching: Quenching metal can lead to warping if done improperly. A sudden drop in temperature can stress the metal, leading to undesirable shapes post-quench. Learning to control cooling rates can minimize this issue.
As you journey through the intricacies of blacksmithing, encounters with these challenges will sharpen your skills. Embracing failures while avoiding common mistakes will ultimately lead you on a path to mastery in the art of shaping metal.
Finale: The Art of Blacksmithing
As we reach the end of our exploration into blacksmithing, it becomes clear that this craft is not just about shaping metal; it embodies a blend of artistry, tradition, and practical skills. Blacksmithing encourages hands-on learning, where failure and success go hand in hand, shaping the smith just as much as the metal on the anvil.
Reflecting on the Journey
Reflecting on the journey of blacksmithing means taking a step back and admiring the hard-earned progress. Beginners often start with simple projects, like hooks or nails, and their growth can be overwhelmingly gratifying. Each piece crafted signifies progress — not just in technique, but in understanding the material.
- Every mistake is a lesson: It is in these errors where learning occurs. Whether it’s a crack forming in steel during cooling or a piece that didn’t quite meet the intended design, each setback teaches resilience, patience, and creativity.
- Celebrate small victories: From forming a perfect taper to achieving just the right heat, every moment deserves recognition. Those moments of satisfaction fuel motivation for the next challenge.
- Connect with others: Joining communities, whether online or in local workshops, offers perspective. Enthusiasts share tips, tricks, and showcases of their work, broadening one’s understanding and inspiration.
Future Perspectives in Blacksmithing
The landscape of blacksmithing is shifting, and it's integral to stay aware of emerging trends. Modern technology is carving new paths, marrying the old with the new in remarkable ways.
- Digital tools and 3D printing: Some smiths are dabbling in design software, creating intricate patterns before ever touching the metal. The 3D printing of tools and prototypes provides an innovative approach that traditional techniques alone cannot offer.
- Sustainable practices: The call for green materials is growing loud. Blacksmiths now look toward recycling and repurposing metal, making conscious choices about their material sources. Sustainability is becoming crucial in ensuring the craft evolves without harming our environment.
"Innovation in blacksmithing is not just about tools; it is about the mindset."
- Education and skill-sharing: Workshops are popping up across the globe, promoting skill-sharing among smiths of all levels. This exchange of knowledge enhances the community and opens doors for those who may be intimidated by the craft.
- Fusion of crafts: The crossover between blacksmithing and other artisanal crafts, such as woodworking or leatherworking, is inspiring new designs and methods in metalworking. It shows that collaboration can lead to innovation where ideas flourish.