Unveiling the Intriguing Universe of 3D Printed Characters
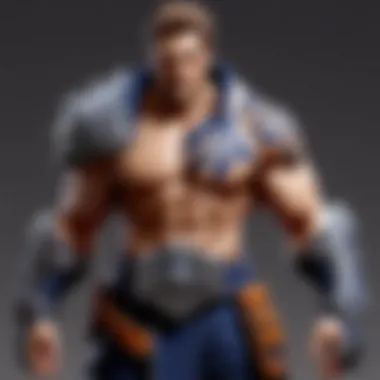
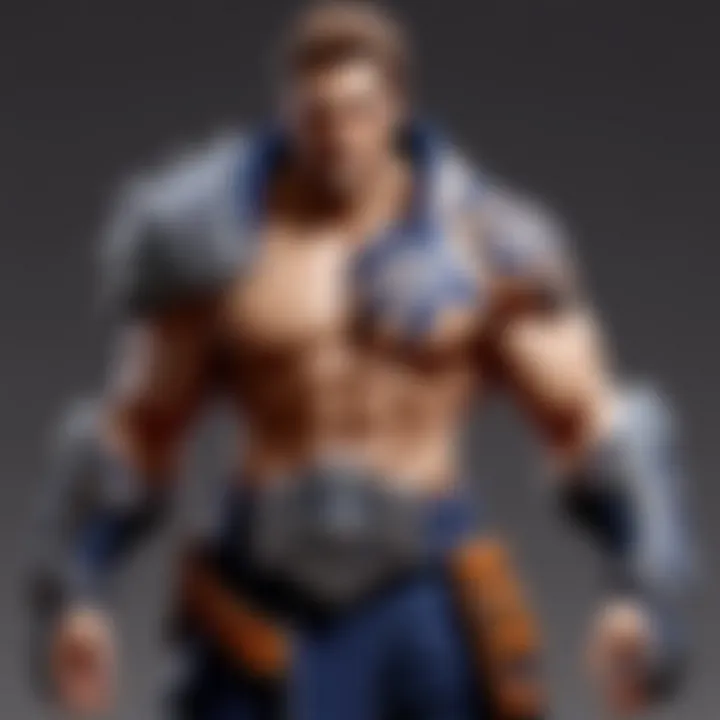
Game Updates and Patch Notes
This section delves into recent updates and patch notes by Blizzard, offering an overview of the latest developments in their games. A detailed breakdown of patch notes and changes is presented, highlighting the modifications made to gameplay elements. Furthermore, the analysis delves into the impact of these updates on the overall gameplay experience and the feedback received from the gaming community.
Character Guides and Strategies
Within this segment, readers uncover in-depth guides focusing on specific characters within Blizzard games. Explore tips and tricks aimed at mastering character abilities and unique playstyles to enhance gaming proficiency. Moreover, strategic approaches for effective gameplay and winning strategies are elaborated upon to assist players in achieving victory within the virtual realms.
Community News and Events
This section showcases the vibrant community surrounding Blizzard games, shedding light on various events and tournaments. Highlights of fan-made content and community creations are celebrated, providing insights into the creativity within the gaming community. Additionally, updates on upcoming Blizzard game releases and special events are detailed, keeping enthusiasts informed and engaged with the evolving landscape of Blizzard games.
E-sports and Competitive Scene
Readers are immersed in the competitive world of e-sports tournaments and competitions dedicated to Blizzard games within this category. Engage with player profiles and exclusive interviews with professional gamers, gaining a closer look at the human element behind competitive gaming. Furthermore, an analysis of the competitive meta and strategies utilized in tournaments offers a deeper understanding of the intricate tactics employed by top-tier players.
Fan Theories and Lore Discussions
Unravel the rich tapestry of storylines and lore embedded within Blizzard games through this section. Delve into interpretations of game narratives and fan theories, providing a fresh perspective on the potential directions of upcoming game storylines. Furthermore, the exploration of hidden secrets and Easter eggs scattered throughout game worlds offers an immersive journey for fans seeking to uncover the mysteries within Blizzard's vast gaming universes.
Introduction to 3D Printing
Understanding the Basics
The history of 3D printing
In the realm of 3D printing, The history of 3D printing stands as a pivotal foundation. This historical account chronicles the origins and early breakthroughs that paved the way for modern-day additive manufacturing. The key characteristic of The history of 3D printing lies in its revolutionary approach to fabricating objects layer by layer, marking a paradigm shift in manufacturing processes. The unique feature of The history of 3D printing is its ability to translate digital designs into physical realities with precision and efficiency. Recognizing the historical trajectory of 3D printing is essential as it highlights the roots of this transformative technology.
The evolution of 3D printing technology
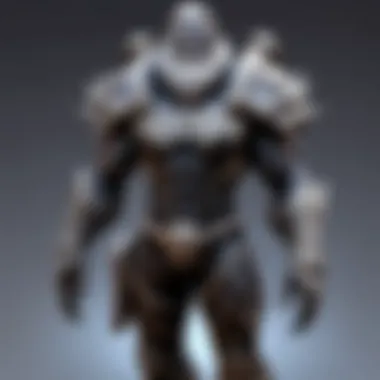
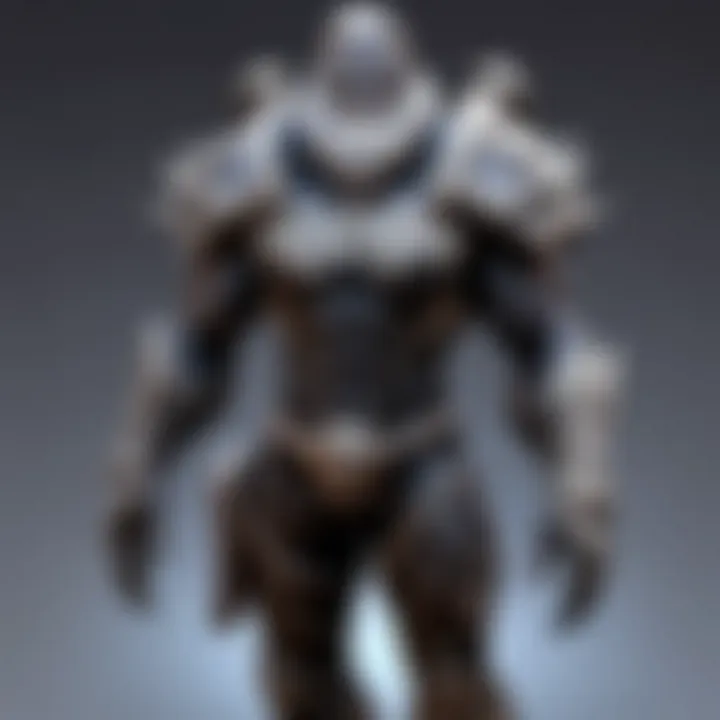
As technology progresses, The evolution of 3D printing technology continues to redefine the possibilities within the realm of additive manufacturing. This segment showcases the remarkable advancements and innovations that have shaped the 3D printing landscape over the years. The key characteristic of The evolution of 3D printing technology lies in its continual refinement and diversification, offering a plethora of techniques and materials for creating diverse objects. The unique feature of The evolution of 3D printing technology is its adaptability to various industries, revolutionizing prototyping, production, and customization processes. Understanding the evolution of 3D printing technology provides invaluable insights into the potentials and limitations of contemporary additive manufacturing.
Types of 3D Printing Techniques
Fused Deposition Modeling (FDM)
Among the numerous 3D printing techniques, Fused Deposition Modeling (FDM) occupies a prominent position due to its accessibility and cost-effectiveness. FDM is characterized by its utilization of thermoplastic filaments that are melted and extruded layer by layer to form objects. This approach offers a practical and efficient means of realizing 3D models with moderate intricacy, making it a popular choice for both enthusiasts and professionals. The unique feature of Fused Deposition Modeling (FDM) is its versatility in material usage, enabling creators to explore a wide range of thermoplastics to achieve desired results. Despite its advantages in affordability and ease of use, FDM also presents challenges in achieving complex geometries and smooth surface finishes.
Stereolithography (SLA)
Moving towards higher precision and surface quality, Stereolithography (SLA) emerges as a sophisticated 3D printing technique that caters to intricate and detailed models. SLA operates on the principle of photopolymerization, where a UV laser solidifies liquid resin layer by layer, resulting in high-resolution prints. The key characteristic of Stereolithography (SLA) lies in its ability to produce fine details and smooth surfaces, ideal for creating aesthetic prototypes and artistic models. The unique feature of Stereolithography (SLA) is its capability to achieve exceptional accuracy and surface finish, setting a benchmark for high-quality 3D prints. However, the limitations of SLA include higher costs and the requirement for post-processing to remove excess resin and achieve the desired aesthetics.
Selective Laser Sintering (SLS)
In the realm of industrial-grade 3D printing, Selective Laser Sintering (SLS) stands out as a versatile and robust technique for producing intricate and functional parts. SLS relies on a high-powered laser to sinter powdered materials, such as polymers or metals, layer by layer, creating durable and precise components. The key characteristic of Selective Laser Sintering (SLS) is its capability to fabricate complex geometries and assemblies, making it a preferred choice for engineering applications. The unique feature of Selective Laser Sintering (SLS) is its proficiency in handling a wide range of materials, including engineering thermoplastics and metal alloys, empowering designers to explore new frontiers in additive manufacturing. Despite its advantages in material diversity and part quality, SLS poses challenges in post-processing, material waste management, and equipment costs.
Creating 3D Printed Characters
Creating 3D Printed Characters is a pivotal aspect of this article, delving into the intricate process of bringing captivating character models to life. The significance of this topic lies in its fusion of technology and artistry, showcasing the potential of 3D printing in the realm of character creation. By exploring the specific elements of character design, detailing, and texturing, readers will gain a profound understanding of the complexities involved in crafting 3D printed characters. This section serves as a comprehensive guide, shedding light on the nuances and considerations essential for producing high-quality and visually appealing character models.
Character Design Process
Conceptualizing character traits
Conceptualizing character traits plays a crucial role in the creation of compelling and memorable 3D printed characters. By carefully outlining the personality, traits, and backstory of a character, designers can imbue depth and emotional resonance into their creations. This deliberate process allows for the development of characters that resonate with audiences on a profound level, fostering strong connections and immersive storytelling experiences. Despite the time and effort required for this phase, the benefits of conceptualizing character traits are abundant, leading to the creation of characters that are not only visually striking but also emotionally engaging.
Digital sculpting techniques
Digital sculpting techniques revolutionize the traditional art of sculpting, providing artists with powerful tools to bring their design concepts to life. By leveraging digital software, creators can manipulate virtual clay with precision, refining details and honing the aesthetic appeal of their characters. The key characteristic of digital sculpting lies in its versatility and efficiency, allowing for quick iterations and adjustments to achieve the desired results. While the digital medium offers unparalleled creative freedom, it also introduces challenges such as mastering the intricate tools and navigating the complexities of virtual sculpting environments.
Software Tools for Character Modeling
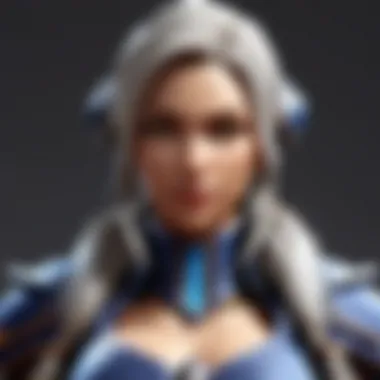
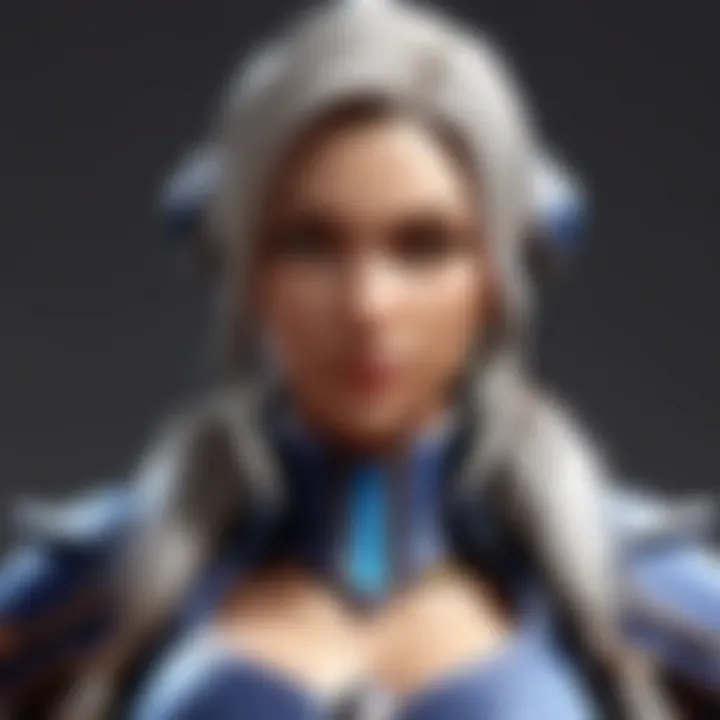
Autodesk Maya
Autodesk Maya stands out as a leading software tool for character modeling, offering a comprehensive suite of features tailored for intricate 3D design projects. Its key characteristic lies in its versatility, enabling artists to sculpt, texture, and animate characters with unparalleled precision. The user-friendly interface and robust capabilities make Autodesk Maya a popular choice among industry professionals seeking to push the boundaries of character design.
ZBrush
ZBrush revolutionizes the digital sculpting landscape with its innovative tools and intuitive interface. The key characteristic of ZBrush is its emphasis on organic sculpting, allowing artists to create lifelike characters with intricate details and textures. This software's unique feature lies in its ability to simulate traditional sculpting techniques in a digital environment, offering a seamless transition for artists familiar with traditional art practices.
Blender
Blender serves as a dynamic software tool for character modeling, catering to artists looking for an open-source solution with robust capabilities. Its key characteristic is its accessibility, providing a wealth of features for character design, rigging, and animation. The unique feature of Blender is its active community support, offering a range of tutorials and add-ons to enhance the modeling process and streamline workflow efficiency.
Importance of Detailing and Texturing
Enhancing realism through textures
Enhancing realism through textures elevates the visual impact of 3D printed characters, adding depth and authenticity to their appearance. The key characteristic of texture detailing lies in its ability to emulate real-world surfaces, creating a tactile and immersive experience for viewers. By meticulously crafting textures that mimic the nuances of skin, fabric, or metal, designers can enhance the overall realism of their characters, making them more believable and visually compelling.
Adding intricate details
Adding intricate details is a labor-intensive yet rewarding aspect of character design, allowing artists to infuse personality and charm into their creations. The key characteristic of intricate detailing is its ability to accentuate unique features, accessories, and embellishments that enrich the character's visual narrative. While the process of adding intricate details requires precision and patience, the end result is a character with depth and complexity, capable of captivating audiences with its meticulous craftsmanship.
3D Printed Characters in Various Industries
Exploring the significance of 3D printed characters in various industries within the broader context of this discourse offers a fascinating insight into the diverse applications of this technology. In gaming and entertainment, these characters play a pivotal role in enhancing virtual worlds and interactive experiences. Their use extends into the fashion and design realm, where customization with 3D printed accessories revolutionizes traditional garment embellishments. Moreover, in the medical field, the development of patient-specific anatomical models and prosthetics showcases the impactful intersection of technology and healthcare.
Gaming and Entertainment
Integration of 3D printed characters in video games
The integration of 3D printed characters in video games revolutionizes the landscape of gaming by introducing meticulously crafted and lifelike avatars. This technological advancement enables game developers to enrich player experiences through intricately designed characters that enhance immersion and storytelling. The bespoke nature of 3D printed characters offers a level of customization unparalleled by conventional methods, providing gamers with a unique and personalized gaming journey.
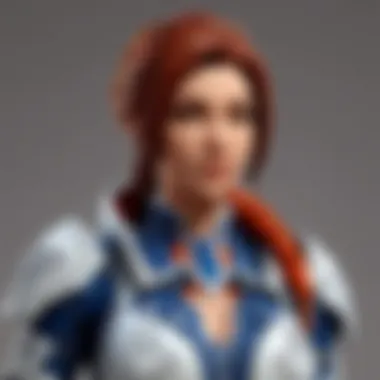
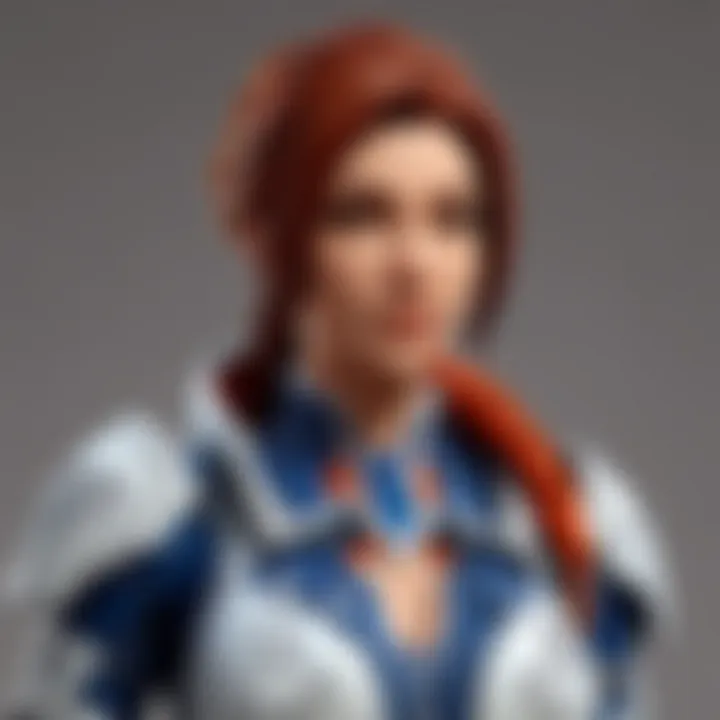
Use of 3D printed models in animated movies
The utilization of 3D printed models in animated movies signifies a groundbreaking approach to character creation and animation. By transitioning from traditional handcrafted models to digitally sculpted and 3D printed counterparts, filmmakers achieve unparalleled realism and detail in their productions. This methodology not only streamlines the production process but also enables the creation of intricate characters with enhanced facial expressions and movements, elevating the visual appeal of animated movies.
Fashion and Design
Customizing clothing with 3D printed accessories
The integration of 3D printed accessories in the realm of fashion and design fosters a new era of customization, where clothing becomes a canvas for artistic expression. By incorporating 3D printed elements into clothing designs, designers can explore unconventional shapes and textures, offering consumers a bespoke wardrobe experience. This innovative approach not only reimagines traditional fashion practices but also promotes sustainability through on-demand production and reduced material wastage.
Unique creations in the fashion industry
3D printing technology has unlocked a realm of possibilities in the fashion industry, enabling designers to push boundaries and unleash their creativity. The creation of avant-garde pieces using 3D printing techniques exemplifies a fusion of art and innovation, leading to the emergence of statement garments that challenge conventional fashion norms. Embracing 3D printing in fashion not only propels design experimentation but also encourages a shift towards sustainable and inclusive practices within the industry.
Medical Applications
Prosthetics and orthopedic implants
3D printed prosthetics and orthopedic implants represent a groundbreaking advancement in medical technology, offering tailored solutions to individuals with complex anatomical needs. By leveraging 3D printing technology, healthcare providers can create prosthetic devices and implants that precisely align with a patient's unique anatomy, enhancing comfort, functionality, and overall quality of life. This bespoke approach to medical intervention underscores the transformative potential of 3D printing in healthcare.
Patient-specific anatomical models
The development of patient-specific anatomical models through 3D printing revolutionizes pre-operative planning and interventional procedures in medicine. These anatomical replicas provide surgeons with invaluable insights into a patient's internal structures, facilitating meticulous surgical plans and enhancing procedural outcomes. Additionally, patient-specific anatomical models assist in medical education and training, offering a hands-on learning experience that bridges the gap between theory and practice in healthcare settings.
Challenges and Future Trends in 3D Printing
3D printing faces numerous challenges and promising future trends, crucial for advancing this cutting-edge technology. At the forefront, overcoming material limitations emerges as a pressing concern. The innovative progress in biodegradable materials unveils a sustainable approach towards manufacturing. These materials offer durability and eco-friendliness, revolutionizing the industry's environmental impact. The biodegradable aspect caters to conscious consumers, fostering a greener production cycle. On the flip side, challenges such as cost and availability hinder mass adoption. However, the enduring aspect lies in their potential to transform production practices effectively.
Enhancing the durability of printed objects stands as another pivotal objective in 3D printing. This aspect targets the longevity and robustness of creations, improving functionality. By incorporating elements that bolster structural integrity, printed objects can withstand wear and tear over time. The improved durability enhances practicality, making 3D printing more viable for everyday applications. Despite advancements, concerns over texture and weight distribution remain, impacting the final output's quality and utility. The quest for optimal durability requires a delicate balance between material properties and printing processes.
Overcoming Material Limitations Biodegradable materials are a game-changer in 3D printing, offering sustainability and functionality in one package. Innovations in biodegradable filaments enable eco-conscious creators to produce environmentally friendly objects. Their renewable nature and biodegradability ensure minimal ecological impact, aligning with the global shift towards sustainable practices. The bio-based composition fosters a circular economy ethos, promoting waste reduction and resource efficiency. However, challenges such as limited color options and print resolution persist, posing constraints for intricate designs. Addressing durability issues in 3D printing unveils a new realm of possibilities for functional prototypes and end-products. Emphasizing material strength and interlayer adhesion enhances the object's resilience, vital for applications requiring robustness. The enhanced durability circumvents brittleness and deformation, ensuring longevity and structural integrity. Despite its advantages, adjustments in printing parameters and post-processing techniques are essential to optimize durability without compromising design intricacies. Striking this balance is crucial for achieving high-performance printed objects that meet industry standards in strength and reliability.
Innovations in Color Printing
In the realm of 3D printing, color plays an integral role in enriching the visual appeal and realism of objects. Multicolor 3D printing technologies introduce a paradigm shift by enabling the production of vibrant, multi-hued models. These advancements open new avenues for creative expression, enriching design possibilities for artists and creators. The versatility of multicolor printing enhances customization, allowing for intricate patterns and vivid gradients. However, challenges related to color accuracy and material compatibility persist, influencing the final output's fidelity. Addressing these constraints requires continuous research and development to refine color mixing techniques and expand the color gamut. Creating vibrant and realistic models: The quest for realism in 3D printed models drives innovations in color accuracy and texture replication. By focusing on creating vibrant and lifelike colors, designers elevate the visual impact of their creations. Vibrancy adds depth and dimension to objects, enhancing their aesthetic appeal. Furthermore, realistic color reproduction enhances the object's authenticity, mimicking real-world counterparts with precision. Despite advancements, limitations in color transition and gradient application pose technical challenges for achieving photorealistic models. Balancing color vibrancy with print speed and resolution remains a delicate undertaking, necessitating a nuanced approach towards achieving optimal results.
Integration with Augmented Reality
Augmented reality (AR) integration marks a significant development in enhancing interactive experiences with 3D printed objects. By overlaying virtual elements onto physical models, AR technology bridges the gap between digital and physical realms. This fusion enables immersive interactions, blurring the boundaries between reality and virtuality. The enhanced user engagement and experiential depth offer novel avenues for storytelling and interactive design. Nonetheless, challenges such as device compatibility and scalability present obstacles in deploying AR-integrated solutions seamlessly. Striking a balance between functionality and accessibility is crucial for ensuring a user-friendly and engaging AR experience. Enhancing interactive experiences: Augmented reality amplifies user engagement and interactivity by superimposing digital content onto real-world settings. This immersive approach transcends traditional boundaries, offering dynamic and compelling experiences for users. By providing interactive elements and real-time feedback, AR elevates the overall engagement levels, making the user experience more immersive and memorable. The blend of physical and virtual worlds creates a symbiotic relationship, enhancing creativity and storytelling possibilities. However, technical considerations such as software integration and content synchronization require meticulous planning to deliver a seamless AR experience. Combining virtual elements with physical models: The synergy between virtual and physical components propels the potential for creating hybrid experiences that merge digital content with tangible objects. By combining computer-generated imagery with physical models, creators craft interactive narratives that captivate and enthral audiences. This integration enriches the overall user experience, offering a harmonious blend of real-world tangibility and digital dynamism. The seamless fusion of virtual elements with physical models expands creative boundaries, enabling innovative applications across various industries. Nevertheless, complexities in content alignment and user interaction pose challenges that necessitate iterative refinement and user testing for optimal results.