Unleashing the Power of Rock Pulverizers: A Comprehensive Guide
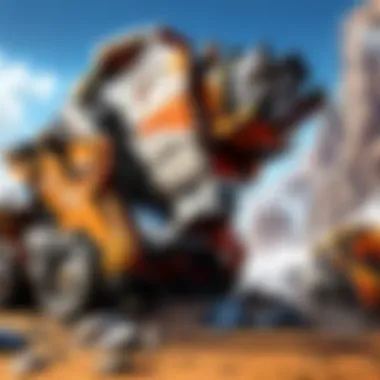
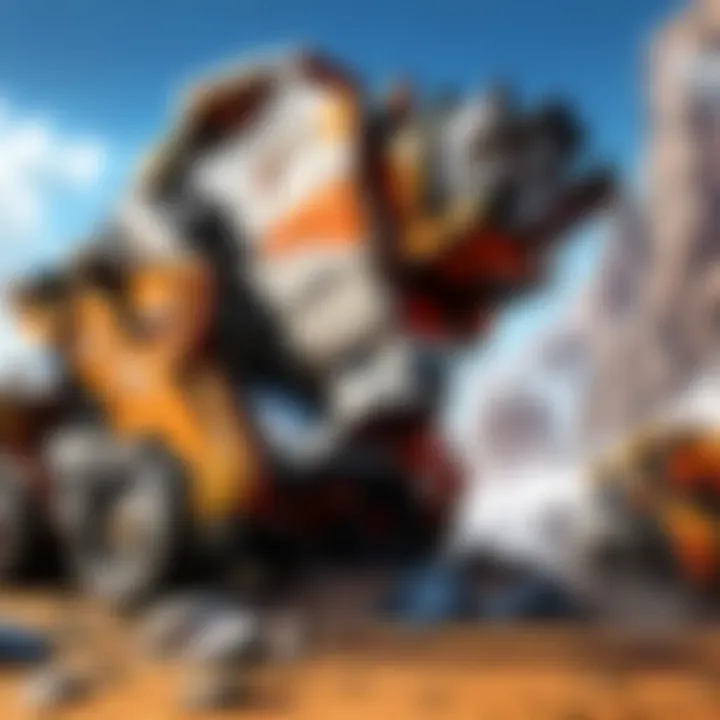
Game Updates and Patch Notes
Rock pulverizers, often likened to the titanic force of nature cradled within mechanized arms, have undergone a recent metamorphosis reflective of the catatonic shifts in the wild ecosystems they inhabit. Updates borne out of the labyrinthine minds of the developers at Blizzard have not only redefined their functionality but unraveled unsuspected facets of their impact. From the meticulous calibration of hydraulic systems to the enigmatic fusion of cutting-edge materials, each change resonates like a seismic wave through the annals of rock pulverization.
Delving into the relentless pursuit of perfection, the patch notes function as a sacred codex, unraveling the mysteries of altered algorithms and cocooned potential awaiting awakening. These chronicles encapsulate the ebb and flow of innovation, laying bare the roadmap of evolution traversed by these monolithic beasts. The minutiae of adjustments, from tadpole shifts in torque dynamics to tectonic shifts in efficiency, construct a symphony of precision mapping the trajectory of rock transformation.
The aftermath of these cyclic revolutions echoes across digital landscapes, eliciting a mosaic of divergent voices harmonizing in discordant unity. Community exaltation blends with dissenting echoes, shaping a cacophony of narratives adorning the mantle of gamer consciousness. Feedback acts as the ether binding developer intent with user perception, crafting a nexus where player experience is both hammer and anvil forging the destinies of the titular machines.
Introduction
Rock pulverizers play a pivotal role in various industries, from mining to construction. Understanding the mechanics, applications, and benefits of rock pulverizers is essential for anyone looking to delve into the world of heavy machinery. This guide aims to unveil the intricate workings of rock pulverizers, shedding light on how they operate, their historical significance, and their environmental impact.
Understanding Rock Pulverizers
The Basic Concept of Pulverization
The basic concept of pulverization lies in the process of breaking down rocks into smaller particles through mechanical force. This fundamental concept is crucial in rock processing, enabling the extraction of valuable minerals and metals from raw materials. The efficiency and precision of pulverization determine the quality of the end product, making it a vital step in various industrial processes. The intricate interplay of pressure, speed, and material composition defines the core of the pulverization process. By controlling these factors, operators can tailor the output particles to meet specific size and shape requirements. Despite its complexity, the basic concept of pulverization simplifies the mineral extraction process, offering a streamlined approach to material processing.
Types of Rocks Suitable for Pulverizing
The selection of rocks suitable for pulverization depends on their composition and hardness. Rocks with high mineral content, such as quartz and granite, are ideal candidates for pulverizing due to their abrasive nature. The choice of rocks significantly impacts the efficiency and effectiveness of the pulverization process, directly influencing output quality and production yields. Certain rocks, like limestone or shale, require specialized pulverizing techniques to ensure optimal results. Understanding the characteristics of different rock types is crucial for operators to select the most suitable pulverization methods. By matching rocks to appropriate pulverizers, industries can enhance overall operational efficiency and product quality.
Key Components of a Rock Pulverizer
A rock pulverizer comprises several key components that work in unison to facilitate the pulverization process. Essential elements include the crushing chamber, hammers or blades, motors, and discharge mechanisms. Each component plays a vital role in breaking down rocks into smaller fragments, with precision and consistency as primary objectives. The crushing chamber acts as the central hub where rocks undergo initial fragmentation, setting the stage for further pulverization. Hammers or blades inside the chamber deliver the necessary impact force to crush rocks effectively, while motors provide the power needed for mechanical operations. Discharge mechanisms ensure proper particle size distribution and output consistency, crucial for achieving desired end-product specifications.
History of Rock Pulverizers
Evolution of Rock Crushing Technology
The evolution of rock crushing technology has transformed the industrial landscape, revolutionizing how raw materials are processed and utilized. From rudimentary stone crushers to advanced pulverizing machinery, the journey of rock crushing technology showcases human innovation and engineering excellence. The continuous refinement of crushing equipment has paved the way for enhanced productivity and resource utilization in various industries. The evolution of rock crushing technology has led to the development of robust and efficient pulverizers capable of handling diverse rock types and densities. Innovations in crushing mechanisms, material durability, and automation have redefined the boundaries of rock processing, opening new possibilities for industrial applications. By tracing this evolution, one can appreciate the ingenuity and ingenuity behind modern pulverizing machines.
Impact of Pulverizers on Industrial Revolution
The advent of pulverizers during the Industrial Revolution marked a significant turning point in material processing and manufacturing. The ability to efficiently crush rocks and extract valuable minerals boosted industrial productivity and spurred economic growth. Pulverizers enabled industries to process vast quantities of raw materials with speed and precision, fueling advancements in infrastructure, machinery, and technology. The impact of pulverizers on the Industrial Revolution resonates in the rapid expansion of industries reliant on mineral resources. Quarrying, mining, and construction sectors witnessed exponential growth and development, thanks to the efficacy of pulverizing equipment. By analyzing this impact, we can understand how pulverizers catalyzed industrial transformation and shaped modern economies.
Significant Milestones in Pulverizer Development

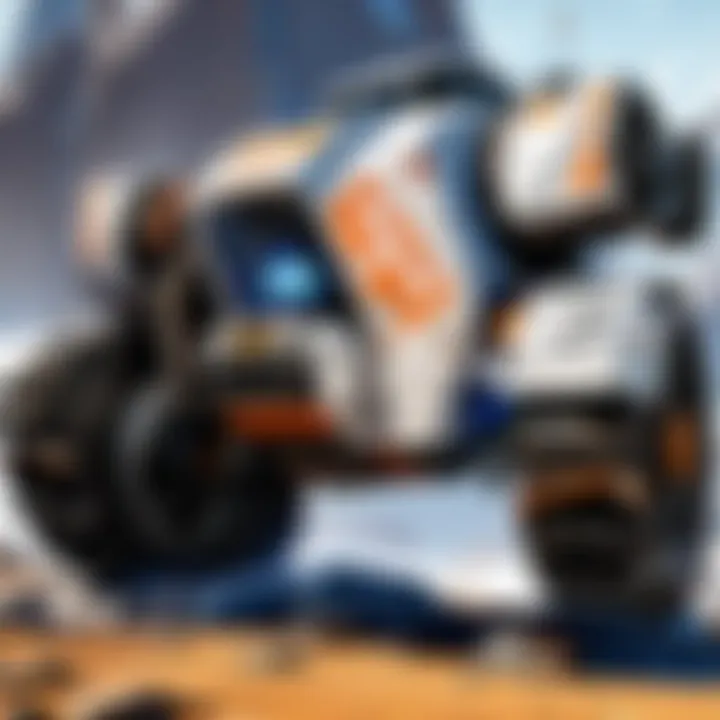
Throughout history, several milestones have defined the evolution of pulverizer development, marking key advancements in rock processing technology. Innovations such as the invention of the stamp mill, the gyratory crusher, and the ball mill revolutionized how rocks were pulverized and minerals extracted. These milestones reflect an ongoing quest for efficiency, reliability, and sustainability in pulverizing operations. The introduction of automated control systems, wear-resistant materials, and environmentally friendly practices has further improved pulverizer performance and longevity. Significant milestones in pulverizer development underscore the continuous quest for technological excellence and operational optimization in the field of rock processing. By acknowledging these milestones, we gain insight into the progressive nature of pulverizer innovation and its impact on industry standards.
Mechanics of Rock Pulverizers
In this section, we delve into the intricacies of the mechanics of rock pulverizers, essential for understanding their operational principles and functionality. The mechanics of rock pulverizers encompass a wide array of components and processes that culminate in the effective crushing of rocks. An in-depth comprehension of these mechanics is crucial for optimizing performance and efficiency in various applications. By dissecting the mechanics, one can appreciate the sophisticated mechanisms at play within these powerful machines.
Crushing Process
Primary and Secondary Crushing
Primary and secondary crushing play a pivotal role in the rock pulverization process. Primary crushing involves the initial breaking down of large rocks into smaller, more manageable sizes, setting the foundation for subsequent stages. Secondary crushing further refines the crushed material, ensuring uniformity and consistency in particle size distribution. The efficiency of primary and secondary crushing significantly impacts the overall productivity and quality of the pulverizing process. While primary crushing sets the stage for further reduction, secondary crushing fine-tunes the output to meet desired specifications, making it a critical step in achieving the desired end product.
Grinding Mechanisms in Pulverizers
The grinding mechanisms within pulverizers are fundamental to achieving the desired particle size distribution. These mechanisms vary based on the type of pulverizer and are designed to efficiently break down rocks into smaller fragments. By understanding the different grinding mechanisms, operators can optimize the pulverization process for specific materials and desired outcomes. The choice of grinding mechanism influences the efficiency and energy consumption of the pulverizer, making it a key consideration in achieving desired grinding results.
Particle Size Reduction Techniques
Particle size reduction techniques in rock pulverizers employ various methods to reduce oversized particles to the required size. These techniques are essential for producing uniform and consistent outputs across different materials. By employing specific particle size reduction techniques, operators can control the granularity and quality of the pulverized material. Understanding the nuances of these techniques is crucial for achieving precise particle size distributions and meeting the unique requirements of diverse applications.
Operating Principles
In this segment, we explore the foundational operating principles that govern the functionality of rock pulverizers, shedding light on the key factors that drive their performance.
Impact vs. Attrition
The choice between impact and attrition as operating principles in pulverizers determines the approach to achieving particle size reduction. Impact pulverizers rely on the high-speed collision of material particles to break them down, while attrition pulverizers utilize frictional forces for size reduction. Understanding the pros and cons of each principle is essential for optimizing pulverizer performance based on the material characteristics and application requirements.
Role of Rotating Hammers
Rotating hammers play a critical role in the pulverization process by delivering impact force to break down rocks. The design and configuration of rotating hammers influence the efficiency and quality of crushing operations. By examining the role of rotating hammers, operators can fine-tune the pulverizer settings to achieve the desired particle size distribution and throughput rates. A comprehensive understanding of the role of rotating hammers is essential for maximizing the performance of rock pulverizers.
Function of Screens and Sieves
Screens and sieves act as critical components in rock pulverizers, determining the final particle size distribution of the output material. These mechanisms help control the flow of crushed material and ensure that the desired particle size range is achieved. By optimizing the function of screens and sieves, operators can produce consistently sized materials suitable for various applications. An in-depth understanding of these components is essential for efficient and effective particle size control in rock pulverizers.
Applications of Rock Pulverizers

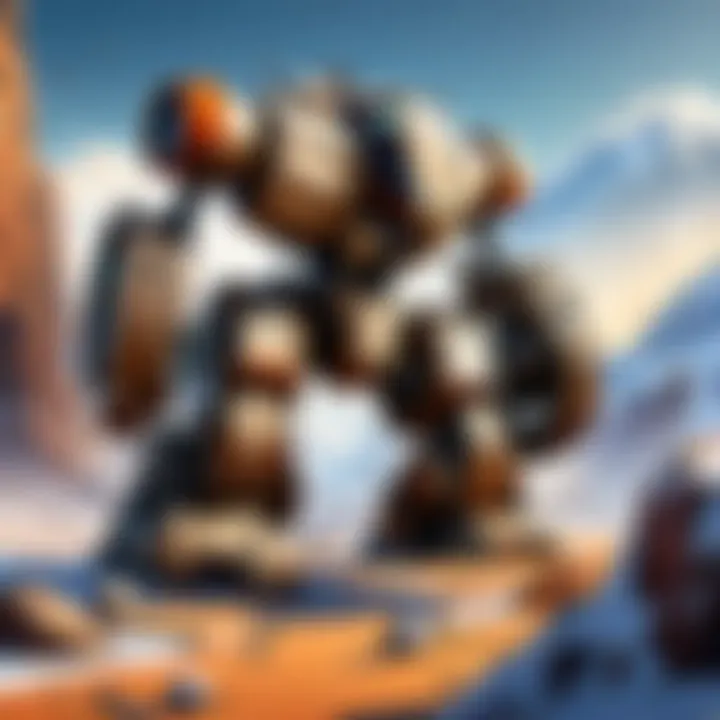
Rock pulverizers play a crucial role in various industries due to their ability to efficiently crush and grind rocks into smaller particles. Understanding the applications of rock pulverizers is essential in comprehending their significance in industrial processes. These machines are extensively utilized in the mining sector for crushing ores and minerals, extracting valuable resources, and enhancing overall mining operations. Moreover, they are instrumental in the construction industry for recycling concrete and asphalt, preparing aggregates for construction, and promoting sustainable building practices.
Mining Industry
Crushing Ores and Minerals
In the mining industry, the process of crushing ores and minerals is paramount for extracting valuable materials. Rock pulverizers excel in this task by breaking down large rocks into smaller, manageable sizes suitable for further processing. The efficiency and precision of crushing ores and minerals using pulverizers significantly contribute to increasing overall productivity and resource utilization in mining operations. Despite occasional challenges in maintaining optimal particle size consistency, the benefits of using rock pulverizers for this purpose are undeniable.
Extracting Valuable Resources
Extracting valuable resources involves separating desirable minerals from ore bodies efficiently and economically. Rock pulverizers facilitate this process by pulverizing rocks containing the desired materials, enabling effective separation and extraction methods. The key characteristic of utilizing rock pulverizers in this context is their ability to handle a wide range of rock types and hardness levels, making them a versatile choice for mineral extraction. While variations in material composition can sometimes pose challenges, the flexibility and adaptability of rock pulverizers make them a valuable asset for extracting resources.
Benefits for Mining Operations
Rock pulverizers offer numerous benefits to mining operations, including enhanced ore processing efficiency, reduced manual labor requirements, and improved safety protocols. By automating the crushing and grinding processes, these machines streamline operations, leading to increased throughput and minimized downtime. Additionally, the precise control over particle size distribution achieved through pulverization promotes optimal mineral recovery and downstream processing. While occasional maintenance and upkeep are necessary, the long-term advantages of incorporating rock pulverizers into mining operations are substantial.
Construction Sector
Recycling Concrete and Asphalt
Recycling concrete and asphalt is integral to sustainable construction practices, reducing waste and conserving natural resources. Rock pulverizers play a key role in this process by crushing recycled materials into aggregate sizes suitable for new construction projects. The high versatility and efficiency of rock pulverizers in recycling applications make them a preferred choice for construction companies aiming to operate in an environmentally conscious manner. Despite intermittent challenges in managing impurities in recycled materials, the overall benefits of utilizing rock pulverizers for recycling efforts are quite significant.
Preparing Aggregates for Construction
Preparing aggregates for construction involves processing raw materials into specific sizes and shapes tailored for various building applications. Rock pulverizers excel in this task by precisely grinding and sizing aggregates to meet project specifications. The unique feature of rock pulverizers lies in their ability to adjust output particle sizes with accuracy, ensuring consistent quality in construction materials. While occasional particle contamination issues may arise, the overall advantages of using rock pulverizers for aggregate preparation outweigh these challenges.
Impact on Sustainable Building Practices
Rock pulverizers have a positive impact on sustainable building practices by promoting material recycling, reducing resource consumption, and improving construction efficiency. By facilitating the production of construction materials from recycled sources, these machines contribute to the circular economy and alleviate environmental burdens associated with traditional extraction methods. The profound implication of rock pulverizers on sustainable building practices underscores their pivotal role in driving towards more eco-friendly and resource-efficient construction processes.
Environmental Considerations
Starting with a crucial aspect of the rock pulverizer industry, environmental considerations play a paramount role in the ongoing discourse. Within this article, we meticulously dissect the importance and impact of environmental considerations when it comes to rock pulverizers. The relentless push towards sustainability and eco-friendliness has led manufacturers and operators to reposition their focus towards greener practices. By delving into how advancements in pulverizer design have spearheaded environmental friendliness, we shed light on the pivotal role these considerations play. Embracing green technologies for pulverizing has not only revolutionized the operational landscape but has also bolstered the industry's sustainability ethos.
Energy Efficiency
Advancements in Pulverizer Design
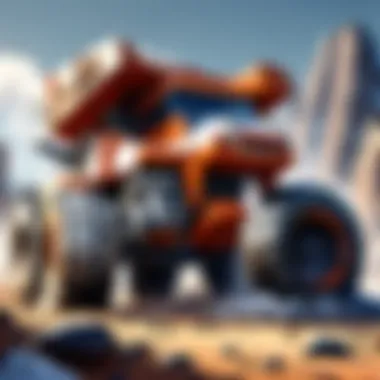
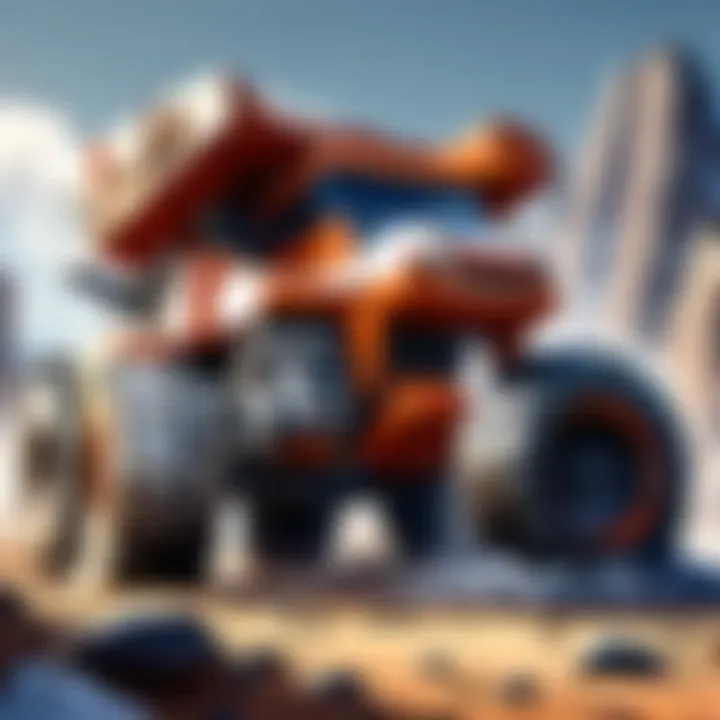
Discussing the finer nuances of advancements in pulverizer design is pivotal in understanding the overarching theme of energy efficiency. These advancements have been instrumental in propelling the industry towards higher efficiency standards. By optimizing the functionality and structural composition of pulverizers, manufacturers have successfully enhanced their energy utilization. The incorporation of cutting-edge technologies into these designs has facilitated a substantial reduction in energy consumption. The integrations of features such as streamlined mechanisms and precision engineering have positioned advancements in pulverizer design as a cornerstone in energy-efficient operations.
Reducing Power Consumption
Examining the facet of reducing power consumption sheds light on the concerted efforts within the industry to minimize energy wastage. Efficient power management has become a focal point for manufacturers, with a concerted push towards implementing strategies that curtail excessive energy usage. By elucidating on the practices and mechanisms aimed at reducing power consumption, we aim to highlight the tangible benefits derived from this approach. From tailored power utilization settings to intelligent power distribution systems, the drive towards reducing power consumption underscores the industry's commitment to sustainable practices.
Green Technologies for Pulverizing
Exploring the landscape of green technologies for pulverizing uncovers a diversified approach towards driving environmental sustainability. The amalgamation of nature-inspired solutions and innovative technologies has paved the way for a greener future in pulverizer operations. Utilizing eco-friendly materials and renewable energy sources, green technologies have revolutionized the pulverizing process. By accentuating the merits and drawbacks of these green technologies within our narrative, we provide a comprehensive outlook on their impact within the pulverizer domain.
Emissions and Waste Management
Evaluating the intricate domain of emissions and waste management brings to the forefront the responsibility that accompanies industrial operations. Addressing the challenges posed by dust and particulate matter, manufacturers have devised stringent protocols and systems to mitigate environmental impact. By delving into the strategies behind controlling dust and particulate matter, we underscore the significance of proactive measures in waste management. Concurrently, the emphasis on recycling waste materials signifies a paradigm shift towards circular economy principles. Expounding on the methodologies and benefits of recycling waste materials accentuates the industry's commitment to resource optimization. Moreover, adhering to environmental regulations serves as a linchpin in fostering compliance and sustainability within the rock pulverizer sector.
Future Trends in Rock Pulverizers
In this section, we delve into the future trends shaping the landscape of rock pulverizers. The advancements in automation and robotics are revolutionizing the way these machines operate, leading to higher efficiency and safety standards. Understanding the significance of embracing these technological trends is crucial for industries reliant on rock pulverizers.
Automation and Robotics (250- words)
Integration of AI in Pulverizing Processes
The integration of artificial intelligence (AI) in pulverizing processes represents a monumental shift in how rock pulverizers function. By harnessing the power of AI algorithms, these machines can optimize their operations by adapting to varying rock compositions in real-time. The seamless integration of AI enhances the accuracy and precision of the pulverizing process, ensuring consistent and uniform output.
Enhancing Safety and Efficiency
Enhancing safety and efficiency in rock pulverizing operations is a top priority for industry professionals. The incorporation of advanced safety features and automation technologies reduces the risk of accidents and improves overall operational efficiency. By streamlining processes and minimizing human intervention, safety protocols are enhanced, and productivity levels are maximized.
Impact of Industry on Pulverizer Automation
Embracing the tenets of Industry 4.0 has a profound impact on pulverizer automation. The implementation of interconnected systems and smart technologies leads to enhanced data exchange and process optimization. By aligning with the principles of Industry 4.0, rock pulverizers can achieve unprecedented levels of efficiency, productivity, and adaptability, positioning them at the forefront of modern industrial practices.
Material Science Innovations (250- words)
Development of Wear-Resistant Materials
The development of wear-resistant materials is a game-changer in the realm of rock pulverizers. By utilizing cutting-edge materials with superior durability and abrasion resistance, the lifespan of pulverizer components is significantly extended. This innovation translates to reduced maintenance costs and increased operational uptime, making it a preferred choice for industries seeking longevity and reliability.
Nano-coatings for Longevity
Nano-coatings offer a revolutionary approach to enhancing the longevity of rock pulverizers. These ultra-thin coatings create a protective barrier against wear, corrosion, and abrasion, preserving the integrity of critical components. The application of nano-coatings prolongs the lifespan of pulverizers, ensuring sustained performance and operational excellence in demanding environments.
Enhancing Performance through Material Research
Material research plays a pivotal role in enhancing the performance of rock pulverizers. By exploring novel materials and fabrication techniques, researchers can optimize the efficiency and output of these machines. The continuous pursuit of material innovation leads to enhanced operational capabilities, cost savings, and environmental sustainability, driving forward the evolution of rock pulverizing technologies.